USTMA Members strive to reduce greenhouse gas emissions throughout a tire's life cycle.
Tire manufacturers recognize our role in mitigating climate change throughout a tire’s life cycle. USTMA members are committed to:
- Manufacturing products that reduce CO2 emissions;
- Research and development of materials with lower carbon footprints;
- Proactive measures to reduce greenhouse gas emissions from our manufacturing facilities; and
- Advancing the circular economy for scrap tires.
Read more about our efforts here.
Rolling Efficiency
Boosting Rolling Efficiency Through High-Tech & Best Practices
Tires are highly engineered products that must meet stringent safety and performance standards. Tire design is an exercise in balance and choice. Rolling efficiency, wet traction and tread wear are three of the key performance factors USTMA members must balance and, traditionally, favoring one attribute came at a cost to the other two, the sweet spot between them depending on the application. Today, thanks to innovative materials and manufacturing technologies, tires with improved rolling efficiency entail fewer performance tradeoffs.
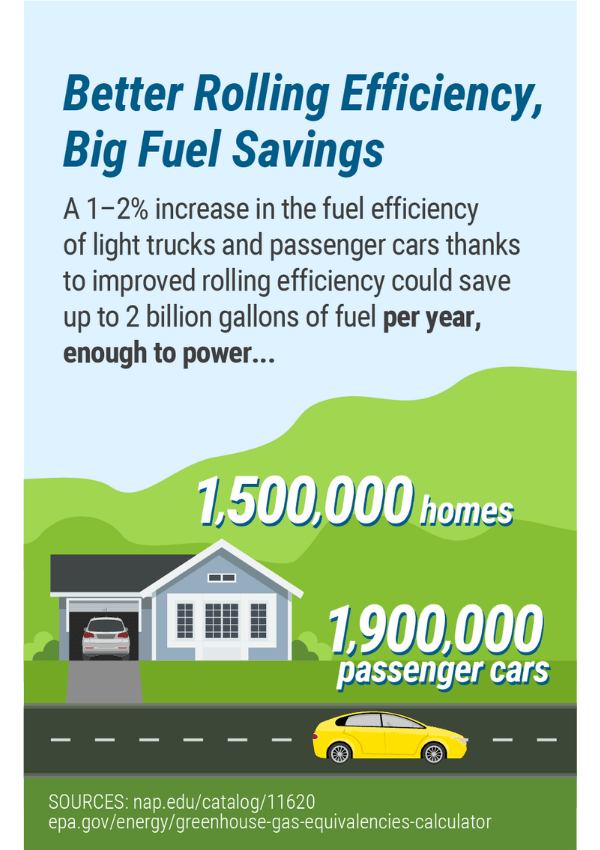
USTMA Member Fuel Mix for 2019
USTMA tire manufacturing facilities are powered primarily by natural gas and, as a result, have a lower greenhouse gas emission footprint compared to other manufacturing sectors. Additionally, tire manufacturers are implementing a variety of strategies and technologies to improve the energy efficiency of their operations and reduce their CO2 emissions.
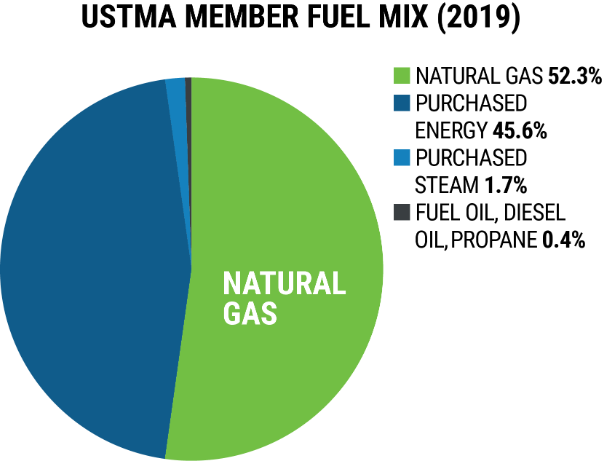
Energy Consumption
Producing higher efficiency tires is relatively more energy intensive, but the front-end energy use is more than offset by the energy savings across the tire’s entire life cycle. U.S. tire manufacturers’ energy consumption increased 7% between 2010 and 2019 with the implementation of new technologies and the construction of new manufacturing capacity. However, because USTMA members are finding energy saving opportunities in other aspects of their operations, total energy intensity — the amount of energy required to produce one ton of product — is growing more slowly than total energy use.
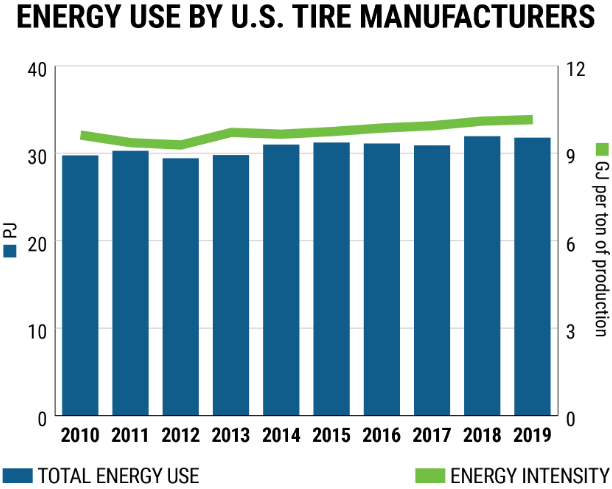
CO2 Emissions
Total emissions of CO2 related to tire manufacturing decreased 15% from 2010 to 2019.
Read more about USTMA’s Climate Principles.
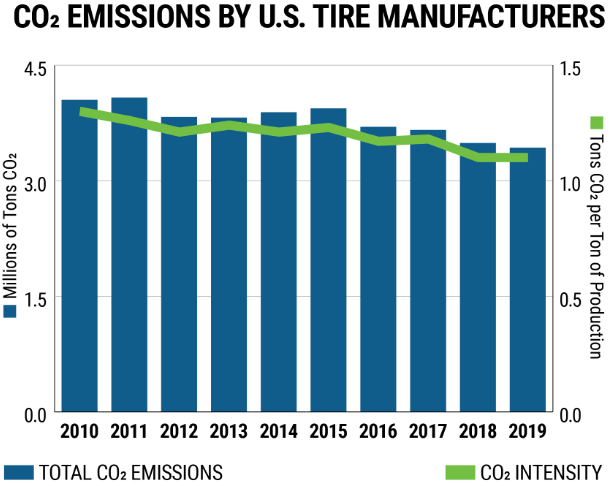
CO2 Comparison to Other Industries
The U.S. Department of Energy data underscores that tire manufacturing remains a low energy-intensive industry. USTMA members have energy efficiency projects which include LED lighting; steam, condensate and compressed air leak programs; and fan upgrades. Read more about USTMA’s Climate Principles.
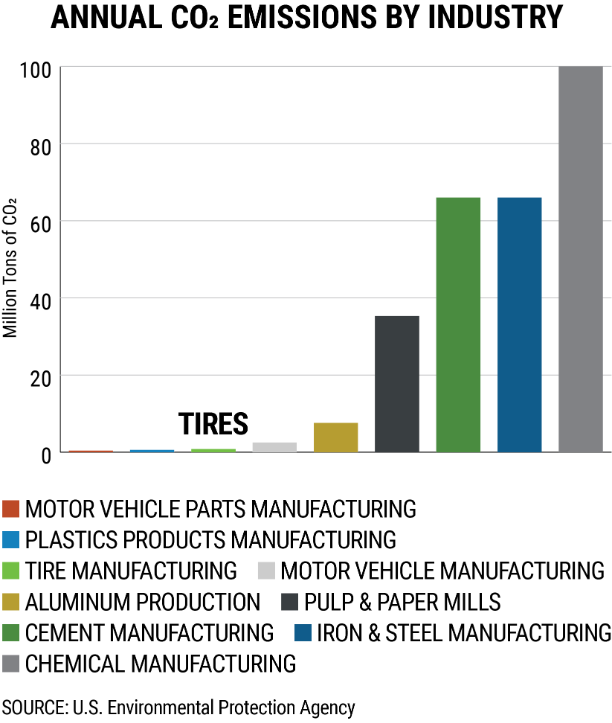
More Circularity = Less CO2
USTMA members support sustainable and circular markets for scrap tires, including markets that reduce CO2 emissions by reducing emissions compared to those associated with the manufacture and transport of virgin materials.
- Rubber modified asphalt made with scrap tires, in addition to offering durability and maintenance advantages, has been shown to contribute lifecycle CO2 emissions at least 32% lower than conventional pavement.
- Pyrolysis of scrap tires to yield recycled carbon black — used to reinforce and manage heat in a tire — produces 81% less CO2 per ton compared to virgin carbon black.2
- In 2019, 36.8% of recovered scrap tires were used as tire-derived fuel (TDF) by cement kilns, pulp and paper mills, and other industrial users. The U.S. Environmental Protection Agency has recognized the biogenic or natural rubber fraction in TDF as carbon neutral, reducing the CO2 emissions profile of TDF and, therefore, the tire’s life cycle. In cement kilns, TDF has an added circularity benefit because the steel belts replace the ferrous oxide that would otherwise need to be added to the cement mix.3
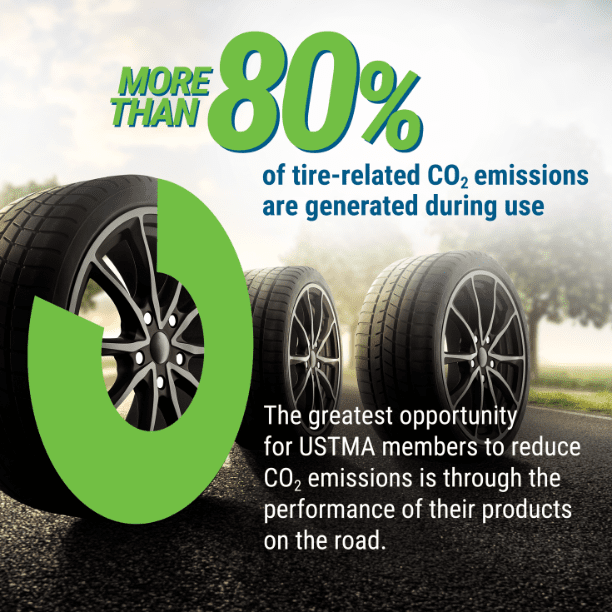